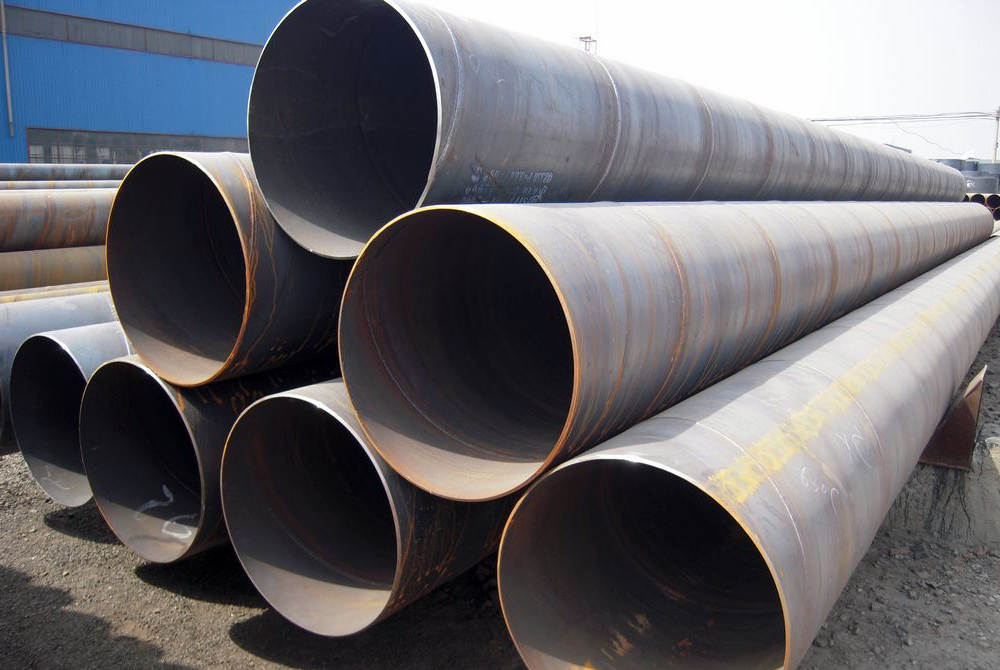
1. SMLS Pipe
Manufacturing process
SMLS Pipe Manufacturing transforms solid steel into seamless hollow tubes.No joints or welding are involved in this process.
This process, often referred to as hot rolling, starts with heating the billet in a furnace at a high temperature. The heated billet, once malleable, is pierced with a mandrel. This starts the hollowing process, creating a thick-walled hollow tube.
This tube is then elongated through a series of rolls, and the wall thickness is reduced by applying controlled pressure in a rotary fashion. The Mannesmann process has improved seamless pipe production techniques. It enables a larger variety of sizes and better control over dimensions and surface quality.
The final product is often annealed to improve its mechanical properties. It is also normalized to improve its microstructure.
Seamless pipes are ideal for high-pressure applications because they have a high level of structural integrity. This process ensures their strength.
View More About SMLS Pipe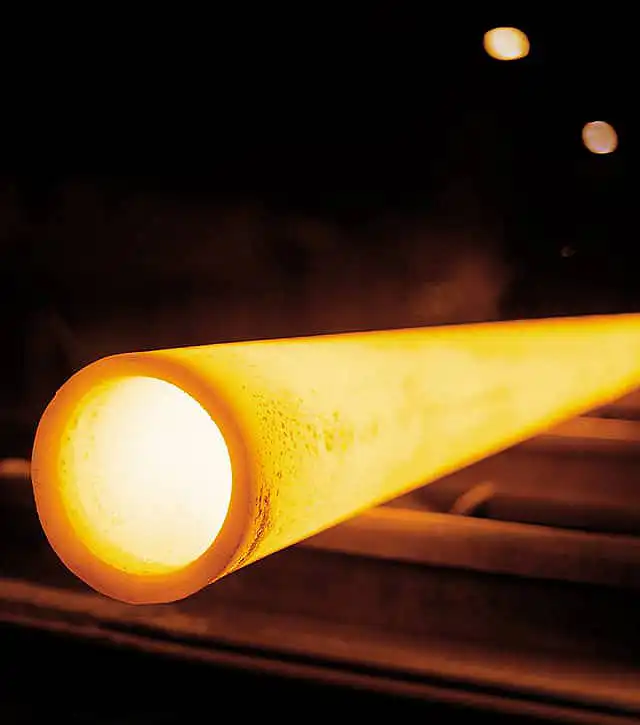
Quality Control
SMLS pipes undergo quality control with rigorous testing of raw materials. This includes analyzing chemical composition and testing mechanical properties.
During production, dimensional checks, surface inspection, and non-destructive testing (like ultrasonic and eddy current tests) are standard. The final products are subjected to hydrostatic tests.
They are also visually inspected to ensure they meet strict standards. These measures guarantee that the pipes meet the necessary standards. They ensure the pipes have the proper strength, resistance to corrosion, and accurate dimensions.
2. ERW Pipe
Manufacturing process
Electric Resistance Welded (ERW) Pipe Manufacturing is a process that produces pipes from strips or coils of steel, known as skelp.
The skelp is uncoiled and trimmed to width before being shaped into a cylindrical form. The cylinder’s edges become charged and generate heat to melt. They fuse together, creating a strong bond without welding material.
ERW manufacturing has seen technological advancements. These advancements include improved control systems. The control systems result in better weld quality. They also lead to more efficient production.
ERW pipes are known for being uniform and precise in size. This makes them suitable for many uses, including oil, gas, and water transmission.
Quality Control
The production of ERW pipes includes strict quality control measures. These measures begin with the inspection of raw materials.
During manufacturing, continuous monitoring of welding parameters and seam quality is conducted. Ultrasonic testing is widely used for detecting any imperfections in the weld.
The pipes are also subjected to hydrostatic tests and visual inspections.
The quality control process is comprehensive. It ensures the structural integrity and leak-proof nature of ERW pipes.
3.SSAW
Manufacturing process
Manufacturing Spiral Submerged Arc Welded (SSAW) Pipes involves a continuous process. A strip of steel called the skelp forms at an angle.
Then, it gets welded along the spiral seam. The skelp goes through rollers that bend the metal at an angle. This introduces internal and external welds using submerged arc welding.
Modern automation and control systems greatly enhance the precision of angle measurements.
They also improve the welding quality of SSAW pipes by ensuring homogeneity. These pipes are frequently used in applications like transporting water. They also have structural purposes in the construction industry.
Quality Control
Quality control in SSAW pipe manufacturing includes checks on the raw material, particularly the steel coil.
During production, continuous monitoring of welding parameters, seam quality, and the pipe geometry is essential.
Non-destructive testing, including ultrasonic and radiographic tests, is conducted to detect any defects.
Final inspections involve hydrostatic testing and visual assessments, ensuring the pipes meet the necessary quality standards.
4.LSAW Pipe
Manufacturing process
Longitudinally Submerged Arc Welded (LSAW) Pipe Manufacturing is a method used for large diameter pipes.
Steel plates are molded into the shape of a pipe and the longitudinal seam is welded both internally and externally using submerged arc welding.
The process has evolved with technologies such as the JCOE (J-ing, C-ing, O-ing, Expanding) process, which has improved the efficiency of LSAW pipe manufacturing.
LSAW pipes have high wall thickness and large diameter.
They also have high-quality welds, making them suitable for heavy-duty applications.These applications are in the oil and gas industry.
Quality Control
Quality control for LSAW pipes begins with the inspection of the steel plates, focusing on their chemical and mechanical properties.
During production, rigorous monitoring of welding parameters and seam inspection is carried out.
Non-destructive testing methods detect defects using ultrasonic and radiographic tests.
The final products undergo hydrostatic testing and visual inspections, ensuring compliance with quality standards.
5. Pipe Fittings
Manufacturing process
Pipe Fittings Manufacturing encompasses various methods like forging, casting, and machining.
Forged fittings are created by heating billets and deforming them under high pressure into the desired shapes.
Cast fittings are made by pouring molten metal into molds of the required shapes.
Machining creates fittings from metal blocks using high precision tools.
Advancements in manufacturing technology have improved precision and efficiency.
These advancements allow for production of high-quality fittings with excellent mechanical properties. These fittings are important for piping systems. They create leak-proof connections in industrial applications.
Quality Control
Quality control in pipe fitting manufacturing includes thorough inspection of raw materials and rigorous in-process checks.
Dimensional accuracy, surface finish, and mechanical properties are tested.
Non-destructive testing methods are used to detect surface and internal defects. These methods include dye penetrant, ultrasonic, and radiographic tests. Final inspections ensure compliance with standards and customer specifications.rectly.
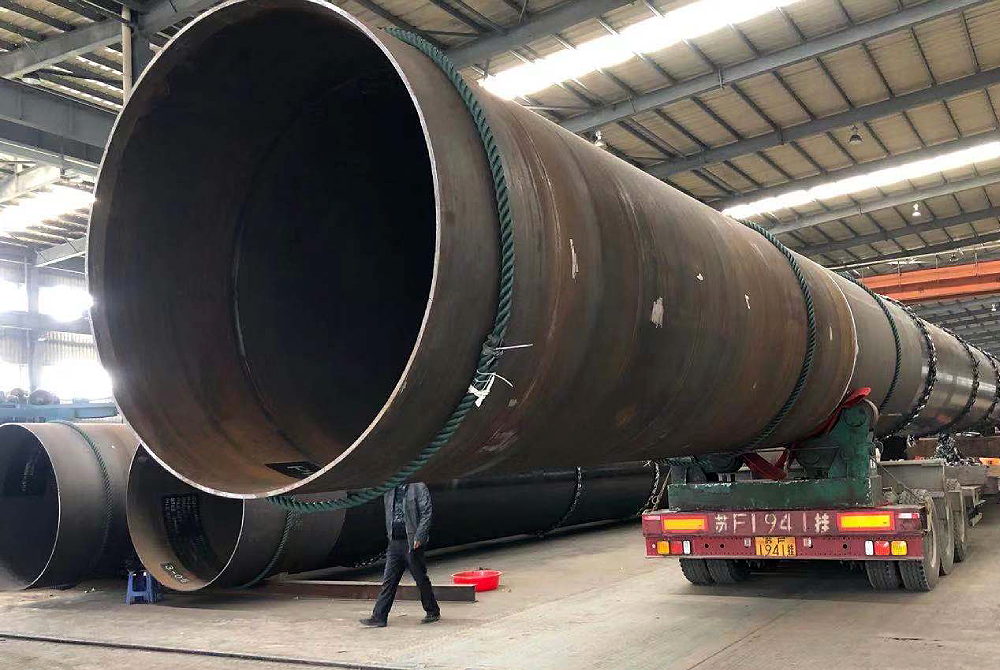
Want to Wholesale Carbon Steel Pipes?
Professional carbon steel pipe supplier for 20 years, exporting steel pipes to overseas markets. Contact us for a free quote and one-on-one service.