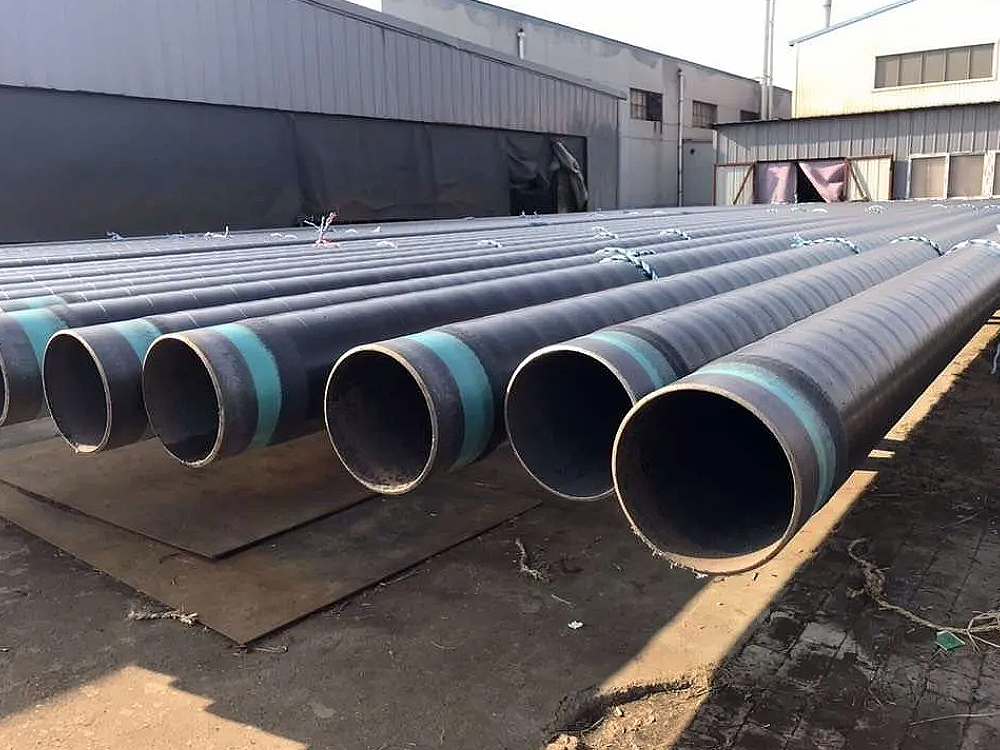
Coated Pipe supplier
Coated pipe has a special material applied to the surface of steel pipe. It’s designed to provide additional protection, improve performance, and adapt to specific application needs.
These coatings are often used to prevent corrosion and rust. They can also insulate or improve specific properties of pipes.
Different types of coated pipes can be used for different applications. For example, some are corrosion-resistant, insulated, or used to transport special substances. Some common coatings include hot-dip galvanizing, polyethylene (PE) coating, polypropylene (PP) coating, and epoxy resin (Epoxy) coating.