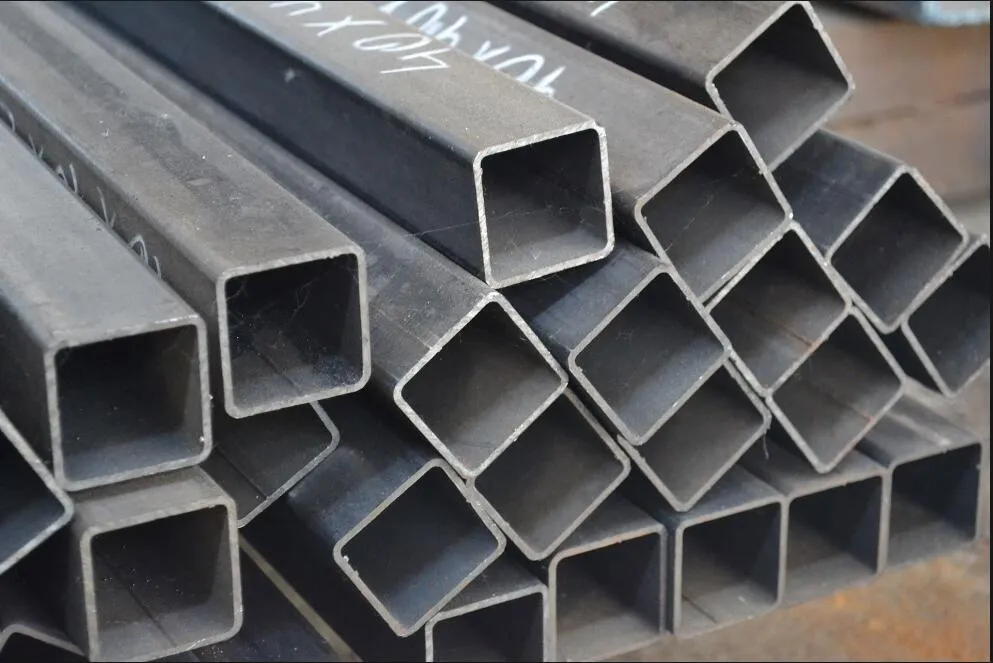
Steel – a pillar in the modern construction industry, comes in different forms to fulfill the requirements. Carbon steel and Mild steel are the most common types of steel with distinct features and applications in the industry.
Carbon steel’s primary component is carbon, with several different components. On the other hand, mild steel is one of the types of carbon steel but has less carbon content. Get ready to enter the world of steel to explore and learn about Mild and Carbon steel in depth.
What is Mild Steel?
Being a low-carbon steel, it is malleable and often used for structural and construction applications.
- Carbon composition: 04 percent to 0.3 percent.
- Mild steel is ductile.
What is Medium Carbon Steel?
Being a medium carbon steel, it is often used in axles, gears, and rails.
- Contains a moderate amount of carbon, around 0.3 percent to 0.6 percent.
- Medium carbon steel signifies a balance between strength and ductility.
What is High Carbon Steel?
It contains more carbon than the previous two types, with 0.6% to 1.5% carbon in it. High-carbon steel is hard and suitable for cutting tools and springs.
Mild vs. medium vs. high carbon steel
Strength
Mild steel is not as strong as higher carbon steel but gives good strength for different applications. It is used where high strength is not required but a balance between strength and properties like formability. Higher carbon steel can show great strength compared to mild steel, making it suitable for enhanced mechanical properties.
Durability
Mild steel is durable and resistant to damage but more corrosion-resistant than higher carbon steel. Coating or galvanizing a surface can increase its durability. Higher carbon steel with added alloying elements can provide better durability, wear resistance, and hardness. However, depending on the specific composition, some may be more prone to corrosion.
Versatility
If affordability is the primary concern, mild steel can be considered for various applications. The ease of fabrication and its applications in multiple sectors, such as construction and automobiles, prove its versatility.
Higher carbon steel material is less versatile due to its hardness and brittleness. However, it is still versatile in specialized applications like cutting tools and high-strength components.
Is carbon steel harder than mild steel?
While analyzing the hardness of mild steel vs carbon steel, it is necessary to account for carbon content in the steel and potential alloying elements.
Carbon steel shows greater hardness than mild steel, credit to its higher carbon content.
In contrast, mild steel has a lower proportion of carbon, resulting in a softer nature. Considering their applications, mild steel is used where hardness is not the goal. Contrary to that, the increased carbon content in carbon steel makes it essential where hardness is required.
Comparing carbon steel vs alloy steel: both are strong, but alloy steel, with added elements, offers enhanced corrosion resistance.
How Resistant is Carbon Steel to corrosion?
The corrosion resistance of any carbon steel is a critical aspect that may influence its performance.
Mild steel is susceptible to corrosion, especially in moisture. It can rust easily when exposed to harsh environments.
The low carbon content makes it prone to oxidation, forming rust (iron oxide) on the surface. Preventive measures like coating, painting, and galvanizing can increase its corrosion resistance.
The corrosion resistance of carbon steel can vary on factors such as alloying elements and heat treatment. Generally, the increased carbon content prevents corrosion.
Alloying elements such as chromium can significantly improve resistance against corrosion. Stainless steel contains chromium, which provides excellent resistance to corrosion.
Manufacturing Process of Carbon Steel and Mild steel
The production process varies slightly depending on the required steel type and final product. Three main steps:
Primary Process
Steel can be created from recycled materials or combined with new steel through Basic Oxygen Furnace.
Oxygen is instrumental in the steelmaking process. Iron ore and coke, serving as raw materials, undergo a conversion. The molten steel is then cast into molds. That’s how slabs and ingots are formed. As a result, the final product has a high carbon content (0.5 percent).
Secondary Process
It’s creating steel with carbon content that meets the market needs. All necessary changes occur here depending upon the desired steel (having high, low, or medium carbon content).
Electric Arc Furnace (EAF)
Here, the steel composition undergoes modification through selective component additions or removals or, alternatively, by adjusting the temperature.
- Stirring
This technique uses electromagnetic fields to induce turbulent currents in the ladle, effectively segregating non-metallic materials. The aim is to achieve a uniform and well-blended composition in the steel.
- Ladle Furnace
Utilizing a secondary electrode furnace ensures precise temperature control and the accurate introduction of alloy components.
- Ladle Injection
To induce the stirring phenomenon, inert gas is introduced from the base of the molten steel, undergoing heating and ascending through the liquid metal.
- Degassing
The reduction of sulfur content from the product while removing hydrogen, oxygen, and nitrogen. A combination of vacuum technology, injection of inert gases, and precise temperature control techniques are employed to remove gases from liquid steel in a degassing process.
- Adjustment of composition
Achieving Stirring through the injection of argon gas in a sealed steel bath with oxygen blowing.
Deoxidizing steel
Controlled removal of oxygen can be crucial to change the characteristics of the final product.
- Rimming Steels
Non or partially-deoxidized steel
- Capped steels
Mold caps prevent carbon monoxide production
- Semi killed steels
0.15- 0.3% carbon, Partially deoxidized
- Killed steels
Completely deoxidized with carbon up to 0.15-0.3%
Casting
In casting, liquid steel is poured into separate molds placed on rail cars. To facilitate removal from the Ingots after concretion, ingot molds are tapered. Casting machines help to cast liquid steel into shapes suitable for downstream processing. Ingots are moved to be reheated for hot rolling, and in the casting machine, steel is turned into slabs, billets, and blooms.
Finishing Processes
The finishing process can impact the appearance and performance of the final product.
Rolling
- Product Rolling
To transform solid cast ingots into a usable form, they undergo rolling, where a rotating roller moves faster than the steel, pushing it forward and compressing it.
- Hot Forming
The steel undergoes heating beyond its recrystallization temperature to achieve consistent grain size and uniform carbon distribution.
- Cold Forming
Performed at a temperature lower than recrystallization temperature, strain hardening increases strength by 20%.
Heat Treatment
Heat treatment is employed to alter carbon distribution to modify mechanical properties.
- Normalizing
To enhance its strength and hardness, steel undergoes a heat treatment process involving heating above 55°C and beyond the upper critical point. The steel is then uniformly heated and subsequently air-cooled.
- Annealing
In the heat treatment, steel is exposed to the solid solution temperature for thirty minutes and then undergoes a gradual cooling phase. This treatment leads to the development of a steel variant that is both pliable and possesses ductile qualities.
- Quenching
It involves rapid cooling of the steel in water, brine, or oil, yielding tough but brittle material prone to breaking.
Surface Treatment
Approximately 33% of global steel manufacturing incorporates surface coating as a preventive against corrosion.
- Hot dip galvanizing
Through this method, steel undergoes a treatment where it is dipped into a heated zinc bath, resulting in the application of a zinc layer. Aluminum is introduced into the zinc solution to enhance the coating’s integrity and prevent breakage.
- Electrolytic galvanizing
The deposition of zinc layer on steel through electrolysis gives a more precise and controlled thickness.
Downstream Secondary processing
Downstream entities refine raw steel materials in the production continuum, shaping them into finalized products. Generally, it includes machining and joining and the removal of surface metal with machine tools and welding.
Cost of Carbon Steel
Mild steel is a low-carbon variant that is generally more affordable than certain high-carbon steels. The cost of raw materials affects the overall production cost.
The manufacturing process is chosen, and the alloying elements are used to create different grades of carbon, processing, and fabrication. Every step affects and can increase the overall carbon steel cost.
Mild steel is often made more malleable and easier to work with, potentially reducing processing costs compared to carbon steel.
The choice between carbon steel and alloy steel relies on the application’s needs, with alloy steel providing tailored solutions.
Applications of Mild Steel vs. Carbon Steel
Carbon steel vs steel has diverse applications across different industries. Mild steel, like beams, columns, and reinforcement bars, are widely used in the construction industry. Its affordability and ease of fabrication make it preferable.
Due to formability, mild steel is used in the automobile industry as body panels, chassis, and structural elements. Low-carbon steel pipe and tubing are durable and utilized for structural components.
Carbon steel is used in cutting tools, drills, and blades due to its hardness. In railways, carbon steel is used to construct tracks and components. Carbon steel pipes transport fluids extensively in the oil and gas industry.
FAQs About Carbon Steel vs. Mild Steel
Q1: What are the key differences between Mild steel and Carbon Steel?
Carbon steel has a broad range of carbon content, which gives different levels of hardness and strength, while Mild steel has a lower carbon content, becoming softer and more malleable.
Q2: How does the amount of carbon affect the properties of steel?
A high level of carbon content leads to increased hardness and strength in steel, making it a better option for mechanical properties.
Q3: Why is mild steel more versatile than higher carbon steel?
The versatility of mild steel comes from its affordability and suitability for different applications.
Q4: How can the durability of mild steel be increased?
Coating and galvanizing can increase the life of mild steel.
Q5: What industries use medium carbon steel?
Mild steel is used in axles, gears, and rails to provide strength and ductility.