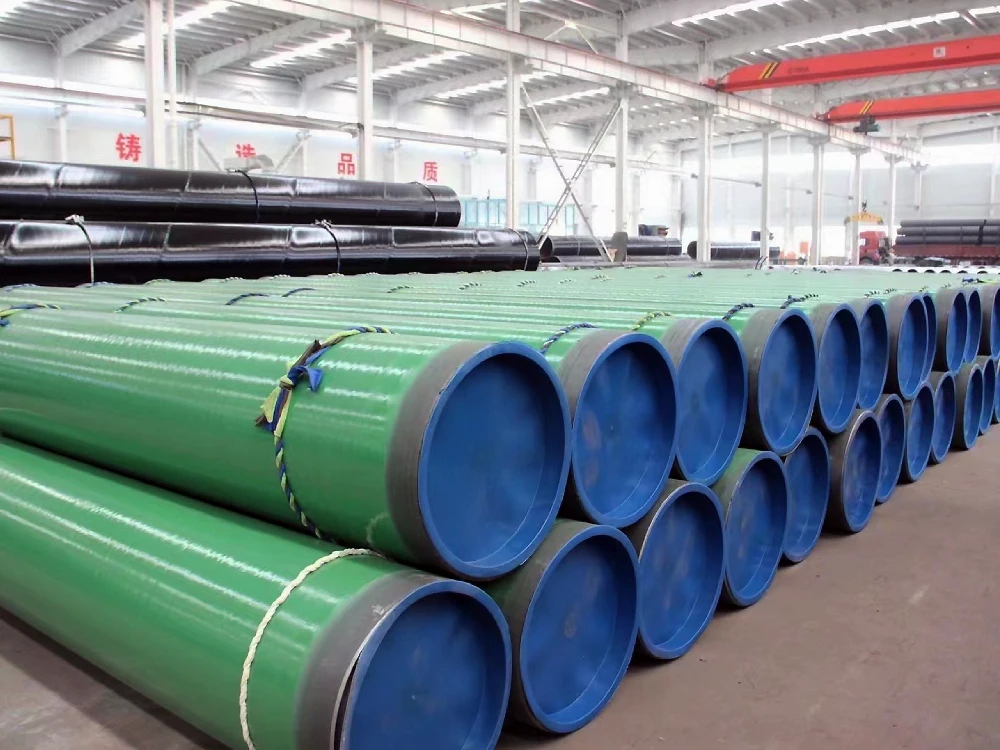
Introduction
Steel pipes are used in different industries for their durability and practicality. Their use often involves exposure to elements and harsh environmental conditions.
Since pipes are made from iron, they are vulnerable to corrosion and rusting. To prolong their lifecycle, a level of protection must ensure they’re safe from natural wear. Pipe coating is a common and effective solution to this problem.
Pipe coating has different types with each one offering a level of protection. You can choose a protective layer based on your application and industry.
Different Types of Pipeline Coating
Steel pipes are strong industrial materials that still corrode if kept in their raw form. That’s why they need extra safeguards from protective coatings. Here are the most common pipeline coatings available in the market.
Fusion-Bonded Epoxy Powder Coating (FBE)
FBE powder coating is a high-performance protective coat for industrial equipment. When applied to steel pipes, it forms a chemically resistant protective layer. This property makes FBE-coated pipes suitable for application in the oil and gas industry due to their durability and high heat resistance.
Applying this coating on steel pipes needs decontamination and preheating of the surface. Before spraying the epoxy, you must free the surfaces from any traces of oil and contaminants. Using an electrostatic spray gun, you can apply it on small and large-diameter pipes.
The next step is to cure the powder coating in an oven at around 392°F- 482°F (200°C-250°C). The curing process melts the epoxy and chemically bonds it to the pipes, creating superb adhesion. FBE coating is a top choice for long-term corrosion resistance and protection.
Pros
- Great temperature tolerance
- High corrosion protection
- Good adhesion
- Chemical resistance
- Low maintenance
Cons
- High initial cost
- Complex application
- Potential brittleness
- Limited repair options
High-Performance Powder Coating (HPPC)
HPPC offers superior protection in extreme conditions. High-performance variants are often used in chemical exposure, high temperatures, and abrasive conditions. They are valued in oil and gas lines, metal refineries, and automotive.
HPPC’s composition is primarily based on polymer resin and some additives and agents. Additionally, it contains polyethylene traces for added protection. Polyethylene content takes credit for protecting the pipes against chemicals and abrasion.
High-performance powder coating is most suitable for pipes with at least a diameter of 14 inches up to 42 inches. They can withstand temperatures ranging from -45 degrees to 85 degrees Celsius.
The downsides of HPPC include temperature sensitivity and complex surface preparation and application.
Pros
- Thermal resistance
- Uniform application
- Cost Effectiveness
- Durability
Cons
- High surface preparation requirement
- Temperature sensitivity
- Application complexity
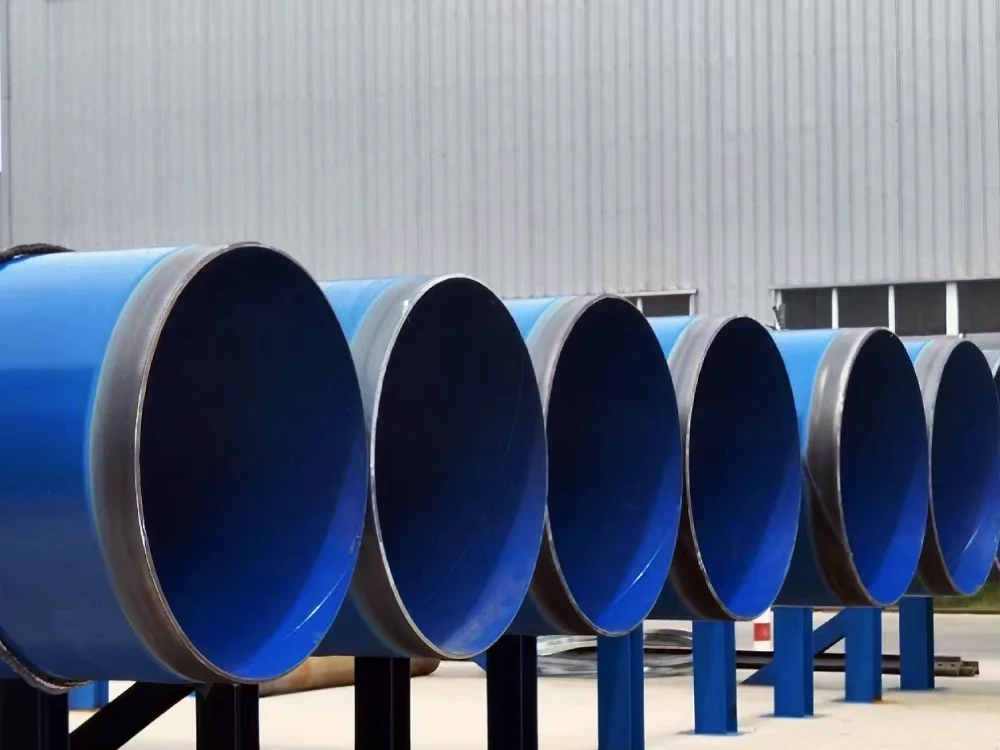
Polyethylene Coating (PE)
PE is a superior powder coating that is valued best for its corrosion and impact resistance. It’s a thermoplastic coating with many purposes rivaling vinyl but beating it in impact handling.
PE applies on the surface of the pipes through fusion bonding, extrusion, or wrapping. Of its many benefits, PE coating boasts superior corrosion resistance. It can handle harsh chemicals, moisture, and corrosive elements. With this, polyethylene coating is standard protection for offshore or water conveyance pipes.
Additionally, PE is particularly strong in handling mechanical damages. It has a high impact rating while maintaining good thermal insulation. It is ideal for retaining the perfect temperature of the pipe content. Like other coating, PE is also low maintenance and versatile to various pipe sizes.
However, it has the potential to degrade quickly when exposed to UV radiation. It also has limited high-temperature resistance and can be more challenging to repair.
Pros
- Impact resistance
- Superb corrosion protection
- Thermal insulation
- Ease of use
Cons
- UV degradation potential
- Thickness limitations
- Repair challenges
- Limited high-temperature resistance
Polypropylene Coating (PP)
Polypropylene coatings are most suitable when high mechanical properties are needed. This includes high-impact and high-penetration resistance. They are also appropriate when high heat resistance is required.
Since the 80s, polypropylene copolymers have protected offshore and in-shore pipelines. It is also used in ordinary pipelines, which has advantages over epoxy resin and polyethylene coatings.
Unlike other coating, PP has a more challenging bonding property. However, such can be addressed through special pretreating of the PP substrate.
Pros
- Resistance to acids
- Good flex resistance
- Lightweight
- Strong anti-corrosion properties
Cons
- Vulnerability to brittleness
- Poor bonding properties

Galvanizing
Galvanization is the most widely used coating method for steel. The process involves coating metals with molten zinc to form a protective layer. In hot-dip steel pipe coating, steel pipes are plunged into molten zinc baths. A metallurgical reaction between the metal and zinc creates a protective layer against rusting.
Galvanizing is a straightforward process and does not need an extra after-treatment process. This cuts the cost without compromising the protection that a galvanized steel gets. Despite its simple process, galvanization offers far more benefits.
As you may notice, galvanization creates a smooth and uniform finish on the metal. A galvanized metal does not need strict maintenance to keep it pristine. Besides the aesthetics, it guarantees durability viable in harsh industrial conditions.
Some drawbacks of galvanization include heavier finished products that can be challenging to install. It is also vulnerable to cracking and chipping over a prolonged duration.
Pros
- Easy application
- Low maintenance
- Smooth and uniform finish
- High corrosion resistance
- Thermal resistance
- Cost-effective
Cons
- Installment difficulty
- Heavy
- Prone to cracking
Conclusion
Each steel pipe coating offers distinct advantages and drawbacks. Steel pipe application remains the most significant factor when choosing a protective layer.
Powder coating is one of the easiest coatings to apply and is more eco-friendly. Others need a more complex coating process but have superb corrosion resistance.
It’s critical to balance the pros and cons of a coating option. Not all have acceptable durability, and some are harder to maintain. Ultimately, your coating should prolong the life of the steel pipe by offering well-rounded protection. It must have standard protection against corrosion, chemicals, and impact. High-temperature resistance is also vital to keeping the pipe’s integrity intact for a long time.