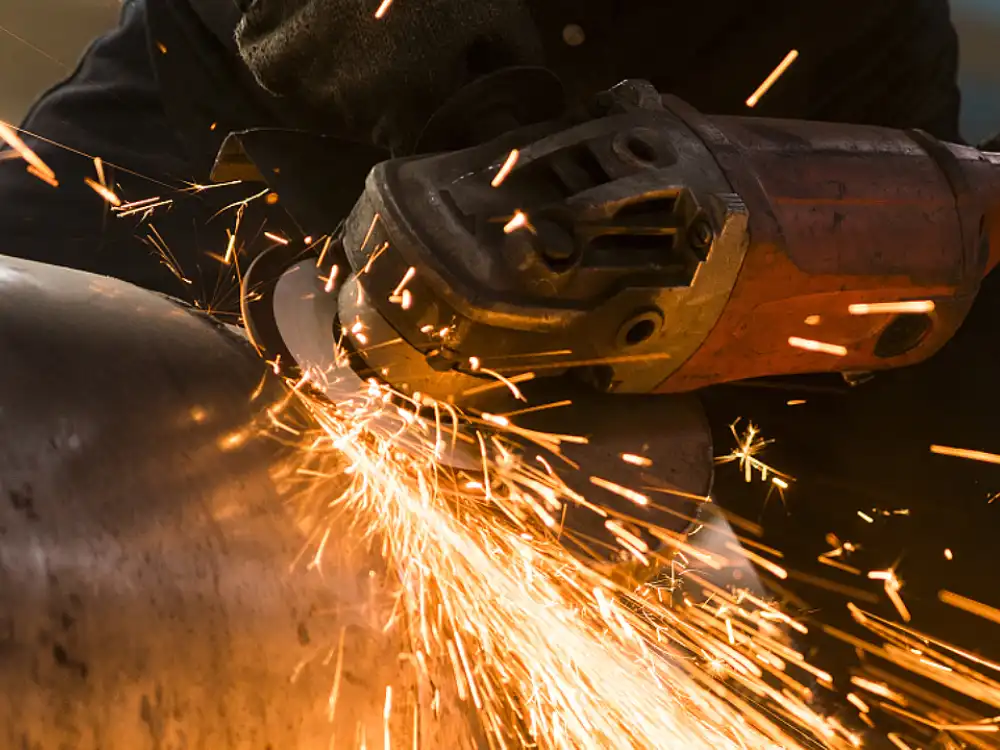
Carbon steel is strong and very durable. As an affordable material, carbon steel can withstand high loads and has good weldability, making it an ideal choice for welding projects.
Although its applications are wide, many engineers and technicians often face a series of challenges in the process of welding carbon steel, including material selection, the complexity of welding processes, and the quality control of welded joints. Its welding performance is directly related to the strength and durability of the final product.
That’s why we want to help you with this article. It will deepen your understanding of the best practices for welding carbon steel. This is crucial for improving welding quality and reducing risks.
What is Carbon Steel?
Carbon steel is an alloy consisting mainly of iron and carbon, with carbon content usually ranging from 0.05% to 2.1%. Due to its excellent strength, durability and economy, carbon steel has become one of the most commonly used materials in the manufacturing industry.
It is not only widely used in construction and infrastructure, but also plays an important role in automobile manufacturing and the energy industry.
Modern carbon steel is affected by small amounts of other alloying elements. These include manganese, silicon, and chromium. Adding them can improve its mechanical properties and welding.
About Welded Carbon Steel
Carbon Steel Type
Carbon steel is defined as steel with a carbon content of less than 2.11% and contains a small amount of Mn, Si, S, P, O, and iron-carbon alloys with other impurities called carbon steels.
According to the C(carbon) content can be divided into:
- Industrial pure iron-carbon content Wc<0.04% iron-carbon alloy;
- Low carbon steel – carbon content Wc<0.25% carbon steel;
- Medium carbon steel – carbon content 0.25%<Wc<0.60% carbon steel;
- High carbon steel – carbon content Wc>0.60% carbon steel;
Welding Processes
Welding Influencing Factors
The higher the carbon content will result in a higher hardness, the less weldability. So, the welding method is different for different carbon content and needs to be adjusted according to the actual.
Alloying Elements: The presence of alloying elements, such as manganese or silicon, impacts the welding process. Knowing the impurity elements level can help find the right welding method.
Other alloying elements, phosphorus, sulfur, oxygen, and nitrogen, also affect weldability. The eutectic temperature of iron and iron sulfide is low (985 ℃). Therefore, during hot working, the eutectic of iron and iron sulfide has already melted due to the processing temperature, which is generally 1150~1200 ℃, resulting in cracks during processing, a phenomenon known as “thermal embrittlement of sulfur.” Therefore, the content of S in steel should be strictly tested. On the other hand, sulfur also tends to cause weld porosity.
Welding Points
Before welding, the following measures can be used to reduce weld defects and improve pipe quality:
- Preheat before welding and maintain the inter-channel temperature during welding.
- Low hydrogen or ultra-low hydrogen welding materials are used.
- Continuously weld the whole weld to avoid interruption.
- Start the arc in the groove, avoid bruising the base material, and pay attention to filling the arc pit when extinguishing the arc.
- Do not form, correct, and assemble at low temperatures.
- Improve cold working conditions as much as possible.
Welding Technology
Arc Welding
Arc welding is the more commonly used method of welding steel pipe. Manual arc welding is suitable for small-batch production, while submerged arc welding is suitable for mass production. Argon arc welding is commonly used in occasions that require high welding quality, such as in the food and pharmaceutical industries.
Gas shielded welding
Gas-shielded welding mainly includes argon arc welding, argon arc argon welding, and argon arc mixed gas welding. These methods in the welding process use inert gas protection to prevent oxygen and nitrogen pollution, thereby improving the quality of welded joints.
High-Frequency Induction Welding
High-frequency induction welding is suitable for producing carbon steel pipes with small pipe diameters. The method generates heat through a high-frequency current, rapidly heats the pipe, and welds it together. This welding method is fast, efficient, and suitable for mass production.
Other Considerations
The weldability of carbon steel decreases with the increase in carbon content because steel with higher carbon content is easily hardened after rapid cooling at the welding temperature.
After hardening, the weld and heat zones are easily affected by the plasticity of the decrease in welding stress under the action of cracking.
Therefore, when welding carbon steel with high carbon content, attention should be paid to slowing down its cooling rate.
In short, carbon steel welding should be based on its different carbon content to take the appropriate process measures.
Low carbon content, such as mild steel, should pay attention to prevent structural constraints and unbalanced thermal stress caused by cracks; high carbon content, such as high carbon steel, in addition to preventing cracks caused by these stresses, should also pay special attention to preventing quenching-induced cracks.