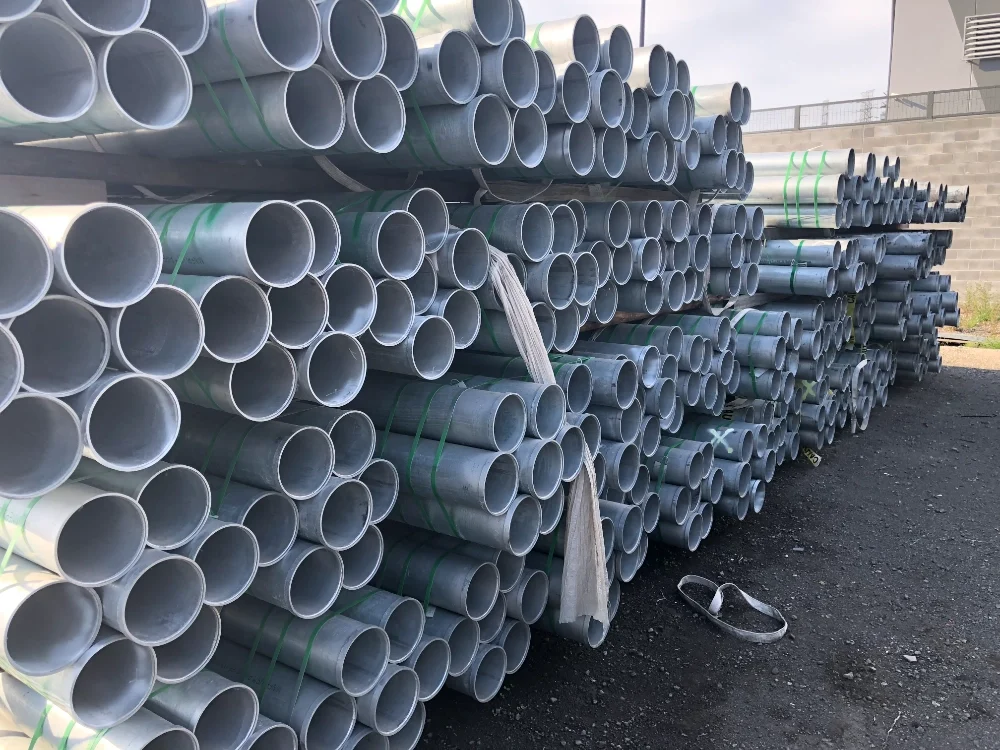
Galvanized Steel Pipe
Galvanized pipes are steel pipes with a layer of zinc on the surface. Through hot-dip galvanizing or electro-galvanizing processes, the steel pipes are covered with a solid anti-rust “protective coat”, which effectively extends the service life by more than 30 years.
The hot-dip galvanizing process dips steel pipes in molten zinc at around 450°C. This creates a strong zinc layer that resists corrosion well. Electro-galvanizing, on the other hand, uses electrolysis. It offers a flexible process and works for many specifications.
Galvanized pipes have both high strength and economy, and are an ideal substitute for stainless steel. They can be widely used in construction, agriculture, industrial pipelines and other fields. Choose UNIASEN’s galvanized pipes and enjoy reliable quality and long-term anti-corrosion guarantee!