ASTM A106 표준이란 무엇인가요?

1. ASTM A106 표준의 범위
ASTM A106 표준은 이음매 없는 강관의 생산 표준 중 하나로, 특히 가스 및 액체를 장거리 운송하는 데 사용되는 이음매 없는 파이프를 지칭합니다. ASTM A106 표준의 파이프는 고온 및 고압 조건에서 뛰어난 성능을 발휘합니다.
2. ASTM A106 표준 적용
ASTM A106은 베벨링, 나사산, 플랜지, 그루브 및 기타 유사한 성형 작업과 굽힘 및 용접에 적합한 이음매 없는 파이프 재료의 일종입니다. 이러한 파이프는 일반적으로 석유 및 가스 정제소, 공기 및 유체 운송, 광물 슬러리 운송, 보일러 및 건설 목적으로 사용됩니다. 이 파이프는 고온 및 고압 조건에서 뛰어난 성능을 발휘하기 때문에 산업 분야에서도 널리 사용됩니다.
ASTM A106 표준의 제조 방법
1. 열간 압연
ASTM A106 표준 파이프를 제조하기 위해서는 먼저 정확한 무게의 빌릿으로 절단된 단단한 철근으로 시작합니다. 그런 다음 천연 가스로 구동되는 회전식 용광로에 넣고 가열하여 1250℃에서 1280℃ 사이가 될 때까지 가열합니다. 그런 다음 가열된 강철은 배럴형 피어싱기로 이동하여 소재를 속이 빈 꽃 모양으로 변형시킵니다. 이는 관리 효과라고 하는 공정을 통해 이루어집니다. 그 다음 중공 블룸은 고급 마감 밀로 이동하여 길쭉하게 만들어집니다. 그런 다음 유도 용광로로 밀어 넣어 균일한 온도로 재가열한 다음, 최종 고객의 특정 요구에 맞게 ASTM A106 파이프 외경을 줄이는 스트레치 감소 밀로 이송합니다.
2. 열처리
이 단계에서는 강관의 경도와 인성을 보장합니다. 이 과정은 오스테나이트 변성 온도 이상으로 파이프를 재가열하는 오스테나이징 용광로에서 시작됩니다. 그런 다음 물 분사를 사용하여 파이프를 약 900℃에서 상온으로 빠르게 냉각시켜 강철의 빠른 상 변형을 일으키는 담금질 공정에 들어갑니다. 이렇게 생성된 ASTM A106 강관의 마린 시딕상은 매우 강하고 부서지기 쉬우므로 템퍼링로에서 변형점보다 낮은 온도로 파이프를 재가열하여 강재의 연성을 회복하고 기계적 특성을 필요한 범위에서 벗어나지 않도록 조정합니다. 그런 다음 파이프는 곧게 펴기 전에 필요한 치수 공차를 달성하기 위해 크기 조정 기계로 이동합니다. 직선화 기계에서는 최종 직선화를 위해 타원형을 만들어야 합니다. 파이프를 최종 상태로 두고 검사 및 테스트를 진행합니다.
3. 마무리
당사의 자동화 라인은 엄격한 테스트와 검증을 수행하여 ASTM A106 강관이 당사의 품질 수준과 고객의 특정 요구 사항을 충족하는지 확인합니다. 먼저, 내부 및 외부의 결함을 감지하기 위해 전자기 검사를 받기 전에 지정된 압력 요건을 충족하는지 확인하기 위해 수압 테스트를 수행합니다. 그런 다음 초음파 검사를 통해 고주파 음파 에너지를 사용하여 벽 두께를 측정합니다. 그런 다음 파이프의 면을 마주보고 경사를 조정하여 나사 가공 프로세스를 시작합니다. 스레딩하는 동안 자동 회전 주축대가 작동하면서 파이프는 고정된 위치에 유지됩니다. 그런 다음 모든 나사산을 육안으로 검사하고 최첨단 검사 장비를 통해 자동으로 치수를 제어합니다. 그런 다음 자동화된 특수 장비를 사용하여 커플링 및 메이크업을 수행하여 최종 ASTM A106 파이프 및 커플링 조인트를 얻습니다. 다음으로 파이프 내부에 막힘이 없는지 확인하기 위해 드리프트 테스트가 수행됩니다. 이제 파이프는 보관 또는 운송 중 부식을 방지하기 위해 래커 및/또는 바니싱 처리를 받습니다. 그런 다음 파이프 트레이서 기술을 준수하기 위한 모든 마킹 요건을 포함하여 열과 파이프 번호를 기반으로 각 파이프를 식별하기 위해 계량 측정 및 스텐실링이 구현됩니다. 마지막으로 파이프는 자동으로 번들링되어 지정된 서비스 센터로 배송되어 고객에게 배송될 준비가 완료됩니다.
ASTM A106 표준과 ASME SA106 표준의 차이점은 무엇인가요?
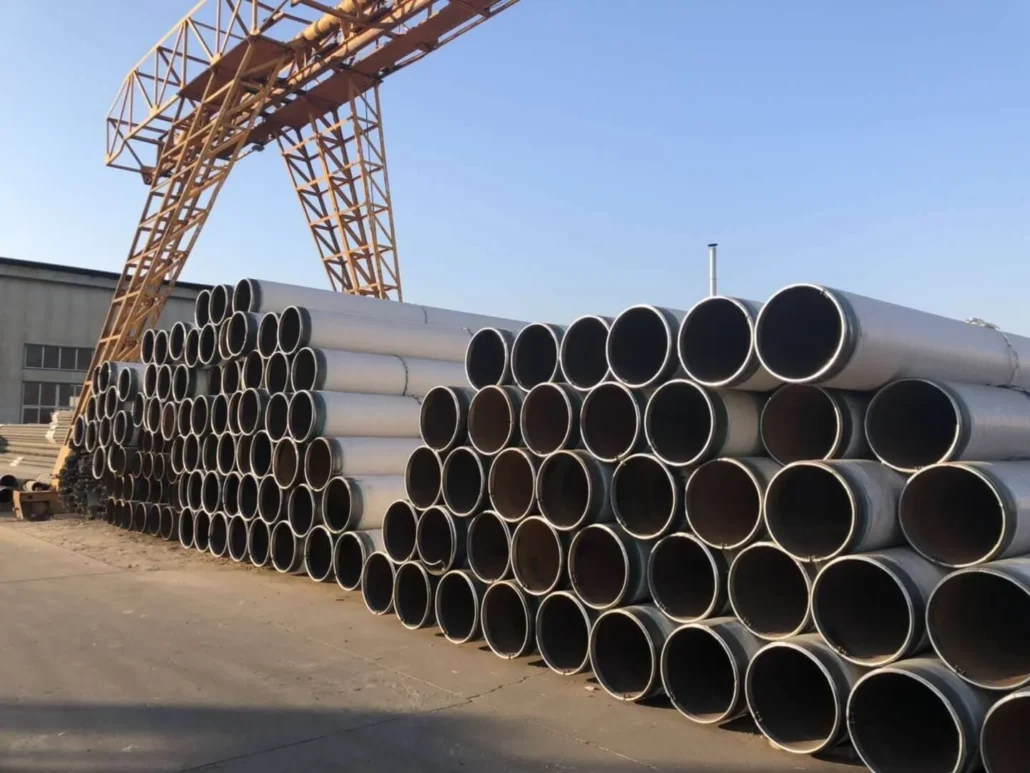
다양한 파이프를 분류하는 방법과 방식에는 여러 가지가 있으며, 그 중 하나가 생산 표준입니다. 심리스 파이프를 구매할 때 시중에서 ASTM A106 표준과 ASME SA106 표준을 흔히 볼 수 있습니다. 둘 사이에 차이가 있을까요? 아니요. A106과 SA106의 재질에는 차이가 없습니다. 차이점은 이 두 표준은 서로 다른 두 기관에서 만든 표준이며 표준 이름을 지정하는 방식이 다르다는 것입니다. ASEM II의 공식판에서는 재료 장에서 SA106이 ASTM A106과 동일하다는 것을 확인합니다. 따라서 서로 다른 이름을 혼동할 필요가 없으며 표준에서 동일한 조항을 공유하고 있습니다.
ASTM A333 표준과 ASTM A106 표준의 차이점은 무엇인가요?

ASTM A333 표준은 파이프 산업에서 흔히 사용되는 또 다른 표준이지만, A333과 A106 표준은 상당히 다릅니다. ASTM A333은 이음매 없는 파이프와 용접 파이프 모두에 대한 표준이며 이 표준에 따른 파이프는 일반적으로 저온 서비스용입니다. A333 파이프는 일반적으로 -45℃ 이하의 건설 또는 운영에서 사용되며 극저온 조건에서 내구성이 우수합니다. 반면, A106은 이음매 없는 파이프, 특히 고온 서비스 전용 표준입니다. A106 파이프는 430℃ 미만의 온도에서 석유 및 가스, 물, 공기 및 난방 수송을 위한 파이프라인으로 사용할 수 있습니다.
API 5L 표준과 ASTM A106 표준의 차이점은 무엇인가요?
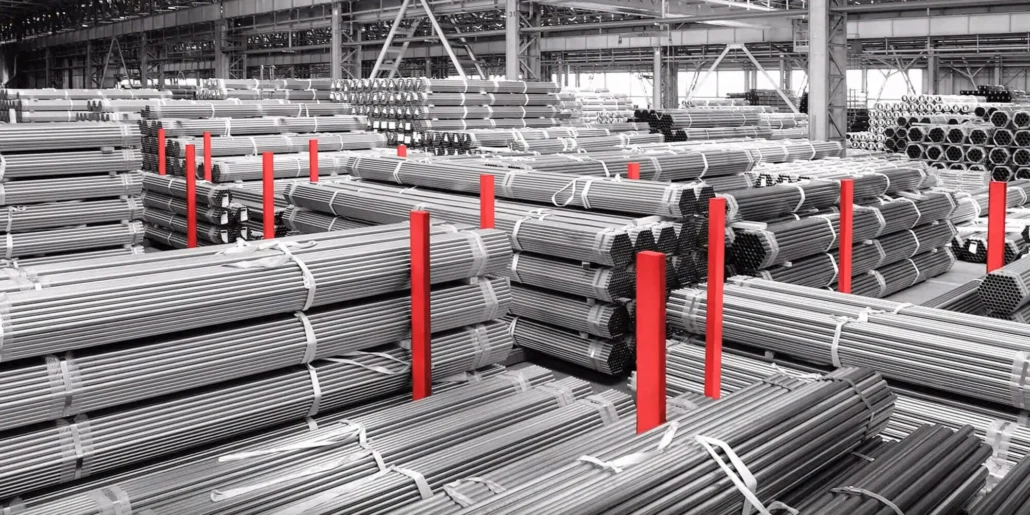
API 5L 표준과 ASTM A106 표준은 모두 파이프 산업에서 자주 사용됩니다. 일부 고객은 기술 요구 사항에 따라 이 중 하나를 선택할 수 있으며, 특히 재고 자재의 경우 구매 시 이중 표준을 요청하는 경우도 있습니다. API 5L은 심리스 파이프와 용접 라인 파이프 모두에 대한 표준이며, 이 표준은 주로 석유 및 가스 산업에 사용됩니다. API 5L과 A106 모두 심리스 파이프에 적용될 수 있지만, APhas는 더 넓은 범위의 강도 수준을 가지고 있습니다. API 5L에는 Gr. A 및 Gr. B 외에도 X42, X46, X52, X56, X60, X65, X70 및 X80과 같은 고강도 재료가 포함됩니다. 또한 API 5L의 품질 요건은 특히 PSL-2 소재의 경우 훨씬 더 엄격합니다.